
CASE STUDY | CORDLESS HAIR DRYER: AIMANT

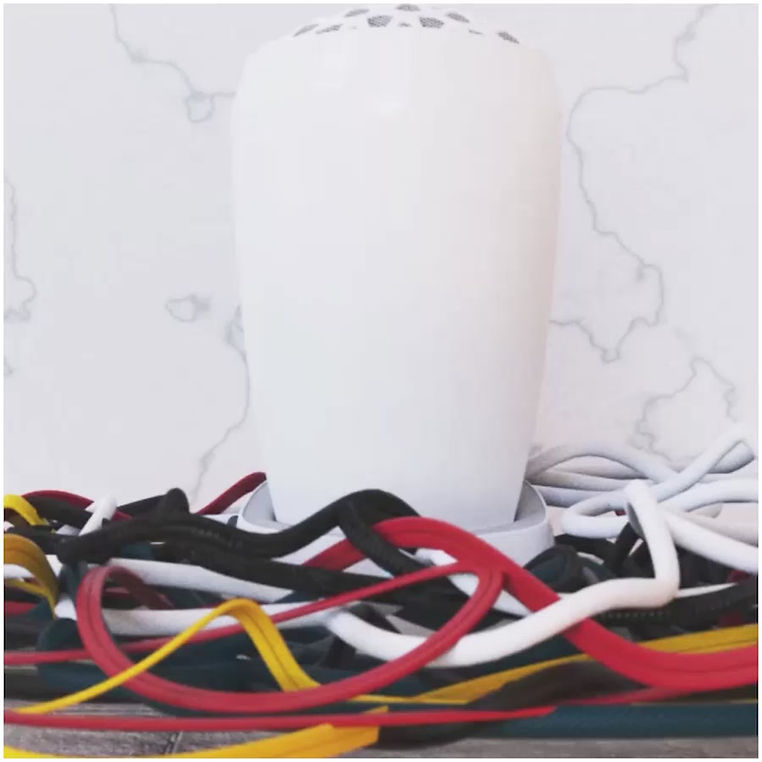
THE CHALLENGE:
The power cord was a once-necessary feature that, now, with innovations in battery technology, charging, and heating element may soon be viewed as an obsolete remnant in the evolution of the appliance.
THE INSIGHT:
Identifying issues with the appliance’s user experience highlights a need improvement. Removing the power cord prompts exploration of battery-powered solutions. A folding or collapsible design significantly reduces storage footprint and offers charging orientation on its base.
THE DELIVERY:
The Aimant Project created an elegant solution to the tangle cords of everyday appliances. Through rigorous design conceptual design, technical research, and iterative 3D modeling, the delivered
3D printed prototype sets the hairdryer apart from mundane.
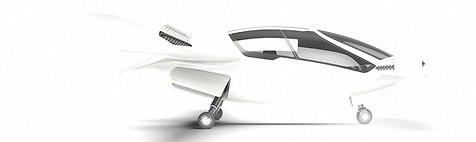
Battery Capacity and Charging Insights
Starting with the hardest problem: how to cut the cord on one of the most power-hungry appliances out there—the hairdryer. A sweep through patents and product lines showed… basically nothing. No real cordless contenders.
Meanwhile, battery tech is catching fire (not literally): faster charging, smaller footprints, longer life. Combine that with slick wireless charging and falling costs, and the cordless future starts to look not just possible—but overdue.
Sometimes, the only thing standing between an old idea and a new solution is the tech finally catching up.
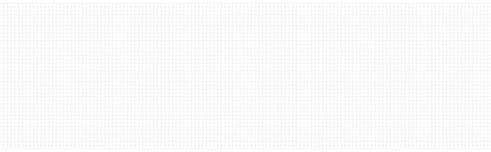




History of Innovation
Pored over a century of design moves—from the first handheld hairdryer in 1920 to modern adjacent tech—to see what had changed, and what hadn’t. Aerodynamic forms like turbines, aerofoils, and fuselages offered fresh inspiration.
With those cues and a handle on the technical constraints, sketching began. The folding form emerged fast—both to shrink the footprint and to nest seamlessly into a charging base. Sometimes, the smartest features are the ones that do double duty.
_edited.png)
Sketching/ Ideating
The idea: a hairdryer so well-designed, it deserves to live on the counter—not hide in a drawer. Early sketches leaned fully into sci-fi vibes, pushing form as far as function would allow. From there, the process became one of refinement—balancing bold shapes with clean utility and building visual harmony between the dryer and its charging base.
Model Iterations
Stationary pegs provide the axis upon which the handle hinges. The rear intake side of the hairdryer was intentionally created larger than the front exhaust in order to accommodate airflow restriction around the handle bay inside the main housing and narrowing the airflow chamber for increased output force.



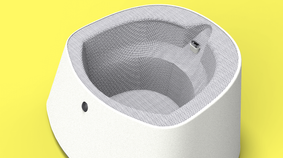
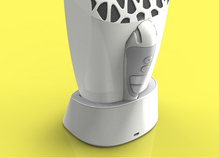

REFINEMENT
The model was crafted so that it looks equally elegant regardless if in use, folded, or charging between uses. The charging base was derived from the inverse geometry of the main housing. This enables a natural fit for the hair drier while charging and ensure a proper charging orientation.
A scratch-free fabric interior protects the hair drier’s polycarbonate surface. The charging base mesh features the similar specifications as the popular Google Home such as hydrophobic and antimicrobial polyester/nylon coating. Overlapping ‘lips’ and annular snap fits were added to the rear mesh and main housing to insure a tight but impermanent fit for prototyping.
Model Iterations
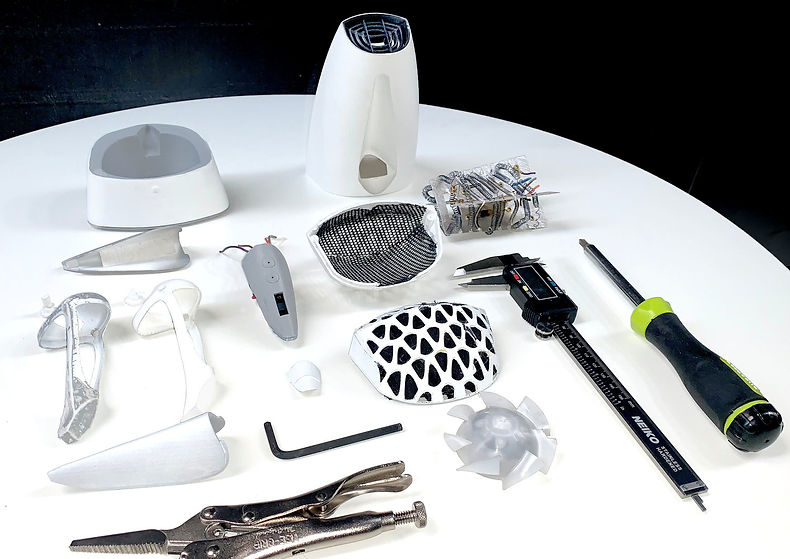
With the careful planning during component research and CAD modeling, I endeavored to materialize a prototype to gauge the accuracy and compatibility of a first round of components including the handle interface buttons and the axis upon which the handle/main housing rotate and if the wiring would successfully cross between the two without impeding the folding function. I exported the solid models of individual components from Rhino with adjusted mechanical tolerances in hopes of getting tight assembly and a satisfying ‘snapping’ together of components.
I sliced the files in Cura 3D Slicer and printed them from my home Ender 3’ 3D printer. With many failures, revisions, and re-calibrations of the printer and model geometry, i was able to achieve a model of outstanding fidelity. Delicate sanding, painting, and hand finishing created a crisp showroom-quality prototype.

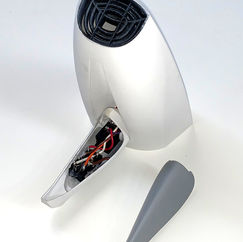

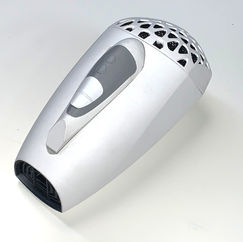

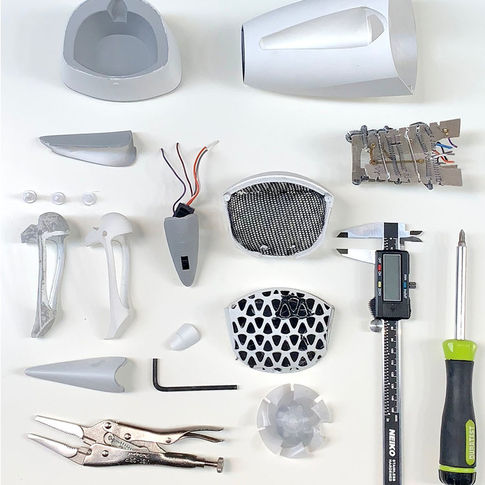
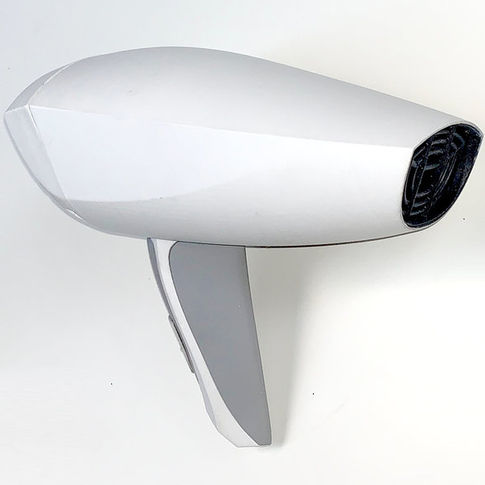

-
Research
-
Sketching
-
Hand rendering
-
Adobe Photoshop
-
Adobe Illustrator
-
Adobe Indesign
-
Adobe After Effects
-
Solidworks
-
Rhino 3D
-
Cura Slicer
-
Ender 3 Firmware
-
Hand finishing/Detailing
-
Keyshot Rendering
-
Keyshot Animation